Papa räumt seit ein paar Wochen seine Werkstattrumpelecke auf. Dabei landen sehr viele, spannende Kisten bei mir: „Hier kannst mal schauen, wenns weg kann, dann schmeiss es weg“. Klar bei dem vielen Sammelsorium ist viel dabei, was wirklich weg kann, ein Grossteil der Kleinteile kommt in meine Kisten, manchmal finde ich Dinge bei denen ich keinen Schimmer habe was das ist – und manchmal finde ich auch alte Schätze die Papa schon zu schade zum Webschmeissen waren und die auch bei mir einfach nicht wegkommen werden.
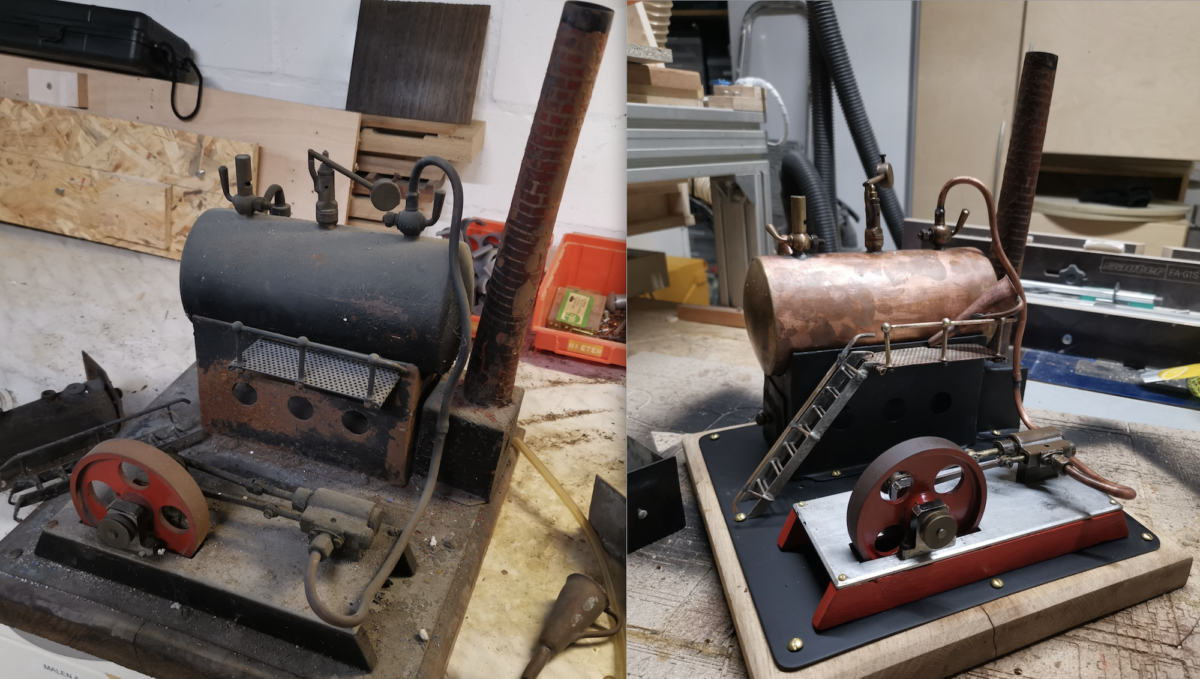
Die Dampfmaschine stand schon lange rum. Ich kann mich erinnern, das ich sie mit Papa oder Opa mal in Betrieb hatte – muss in den 80ern gewesen sein. Danach hat sie sicherlich niemand mehr benutzt, denn irgendwann gab es eine mit Strom und die alte mit Esprit oder Flüssigbrennstoff wurde mehr oder weniger vergesssen. Gebaut hat sie Opa, irgendwann in den 50er oder 60er Jahren. Sie muss also sicherlich über 60 Jahre alt sein.
„Die Dampfmaschine“ weiterlesen